Industry: continuous improvement of teams
The teams at Laïta’s factories are involved in continuous improvement strategies in their everyday work. Christophe, an industrial performance project leader, explains how the staff are constantly striving to do better on the shop floor.
Performance starts at ground level
Christophe, Project Leader, Industrial Performance, Laïta, Ancenis (44)
“The notion of industrial performance is multi-faceted at Laïta. It covers the safety of people and goods, food safety, quality, costs, deadlines, human resources, the environment and innovation. Industrial performance departments support teams and activities to achieve their strategic objectives, which forms part of Passion du LaitÒ, our corporate social responsibility strategy. The staff take part in the continuous improvement and performance strategy as part of their daily work on the shop floor, using tools and methods for progress which we endeavour to standardise so that we all progress together at the same rate. The tools include the 5S’s, a way of organising the workspace based on the principle ‘a place for everything and everything in its place’. There are also problem-solving tools which can help pinpoint the reason why a machine has broken down, for example, and develop a plan of action to make sure it doesn’t happen again in the future.”
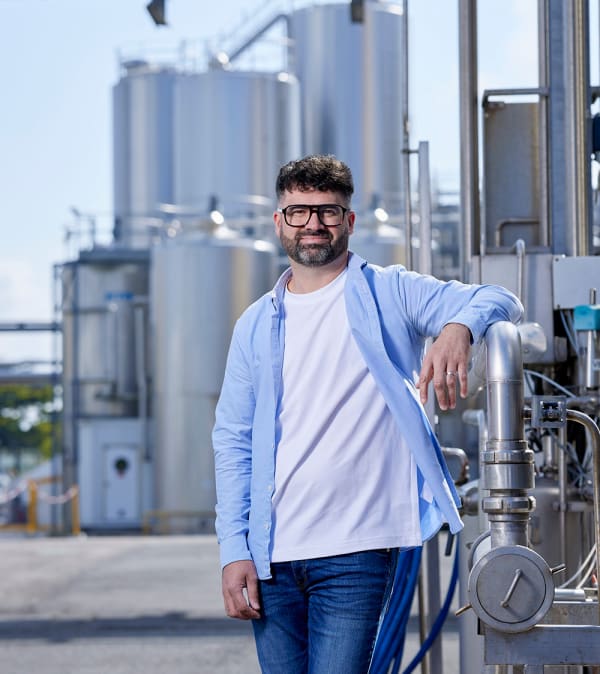
Targeting operational excellence
“We’re also developing visual management tools to facilitate team processes. These communication areas are set up in the actual workplace and consist of visual indicators in red or green that show the status, for example, of the safety cross, line productivity and waste monitoring. Team members can see at a glance if the department is achieving its objectives and identify actions to be carried out to get them back in the green, together with their team leaders. The staff can also see how much their daily work has contributed to the performance of their workspace, their shop floor and the company in general. Our industrial performance departments also manage structuring projects to support change. The one we’re currently involved in is the EOL project - Operational Excellence at Laïta - designed to construct and implement a common strategy to drive performance in our activities, our factories and the industry as a whole.”
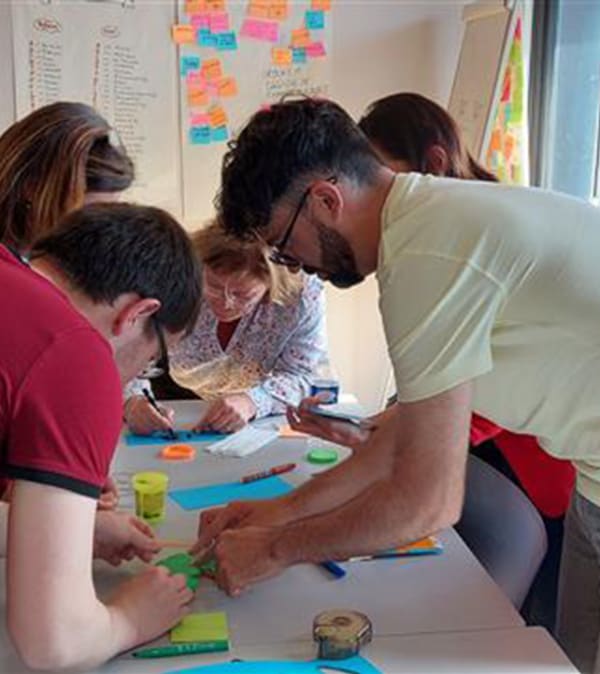
“Laïta operates a common management approach to performance, covering the safety of people and goods, food safety, quality, costs, deadlines, human resources, the environment and innovation.”
![]()
Christophe
Project Leader, Industrial Performance
Explore our other commitments and testimonials
Our other pillars
Committed and passionate
All about our approach #committed
Because our environmental, human and social commitment is a daily reality, we place CSR at the heart of our actions.